Evaluating Different Types of Window Manufacturing Equipment for Optimal Production Efficiency
In the rapidly evolving landscape of the manufacturing industry, achieving optimal production efficiency is paramount for businesses involved in window manufacturing. The right selection of Window Manufacturing Equipment plays a crucial role in streamlining operations, reducing waste, and enhancing overall quality. With a myriad of equipment options available, from automated cutting machines to advanced insulating systems, manufacturers face the challenge of evaluating which technologies best suit their specific needs and production goals.
This blog aims to guide manufacturers through the process of assessing various types of Window Manufacturing Equipment, highlighting key factors that influence performance and efficiency. By understanding the capabilities and limitations of different machinery, businesses can make informed decisions that not only elevate their production standards but also lead to greater profitability. Let’s delve into the essential considerations that will help you optimize your window manufacturing process and stay competitive in the market.
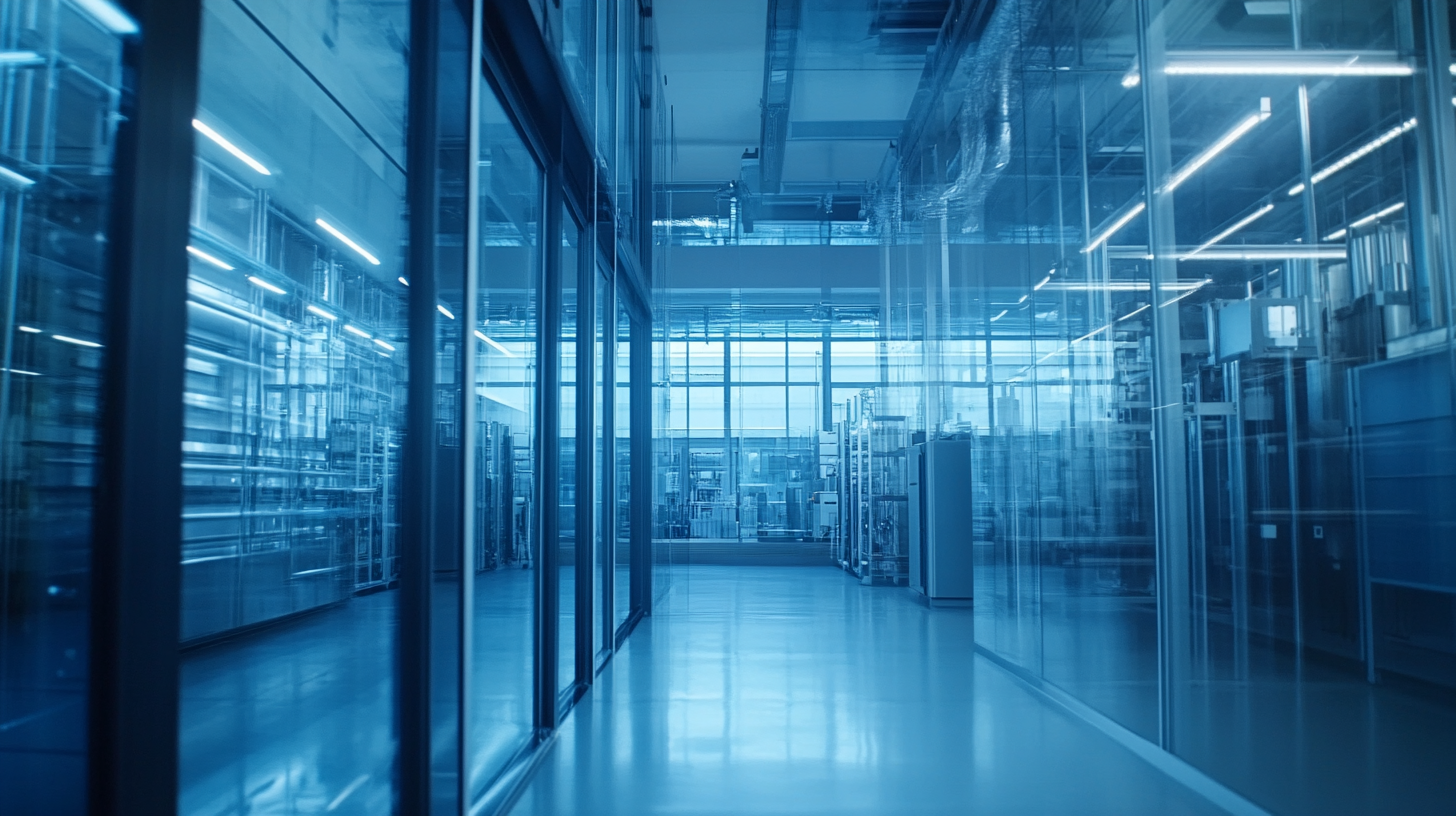
Types of Window Manufacturing Equipment: A Comprehensive Overview
In the window manufacturing industry, the selection of equipment plays a pivotal role in determining overall production efficiency and quality. A comprehensive overview of the various types of window manufacturing equipment reveals several categories, each tailored to specific needs within the production process. Notable equipment types include automated cutting machines, CNC (Computer Numerical Control) routers, and glass lamination systems. Automated cutting machines have emerged as a significant advancement in window manufacturing. These machines enable precise cuts, reducing material wastage significantly. According to a report by the American Architectural Manufacturers Association, companies using automated cutting equipment can experience a reduction in labor costs by up to 30%, while improving cutting accuracy by 25%. This efficiency not only speeds up production times but also enhances quality control, leading to less rework and higher customer satisfaction. CNC routers are another cornerstone of modern window manufacturing. They provide versatility and precision for fabricating complex designs, enabling manufacturers to meet the diverse demands of custom window applications. A study from the National Association of Home Builders highlighted that implementing CNC technology can increase production capacity by 40%, allowing companies to fulfill orders more rapidly and maintain a competitive edge in the market. Additionally, advancements in glass lamination systems have revolutionized window production, especially in terms of safety and durability. These systems ensure that windows resist shattering upon impact, meeting increasing safety regulations and consumer preferences for enhanced protection. Research estimated that over 60% of new residential windows now incorporate some form of laminated glass, reflecting consumers' priority for safety features. By investing in the right equipment, manufacturers can not only optimize their production efficiency but also elevate their product offerings to meet evolving market demands.
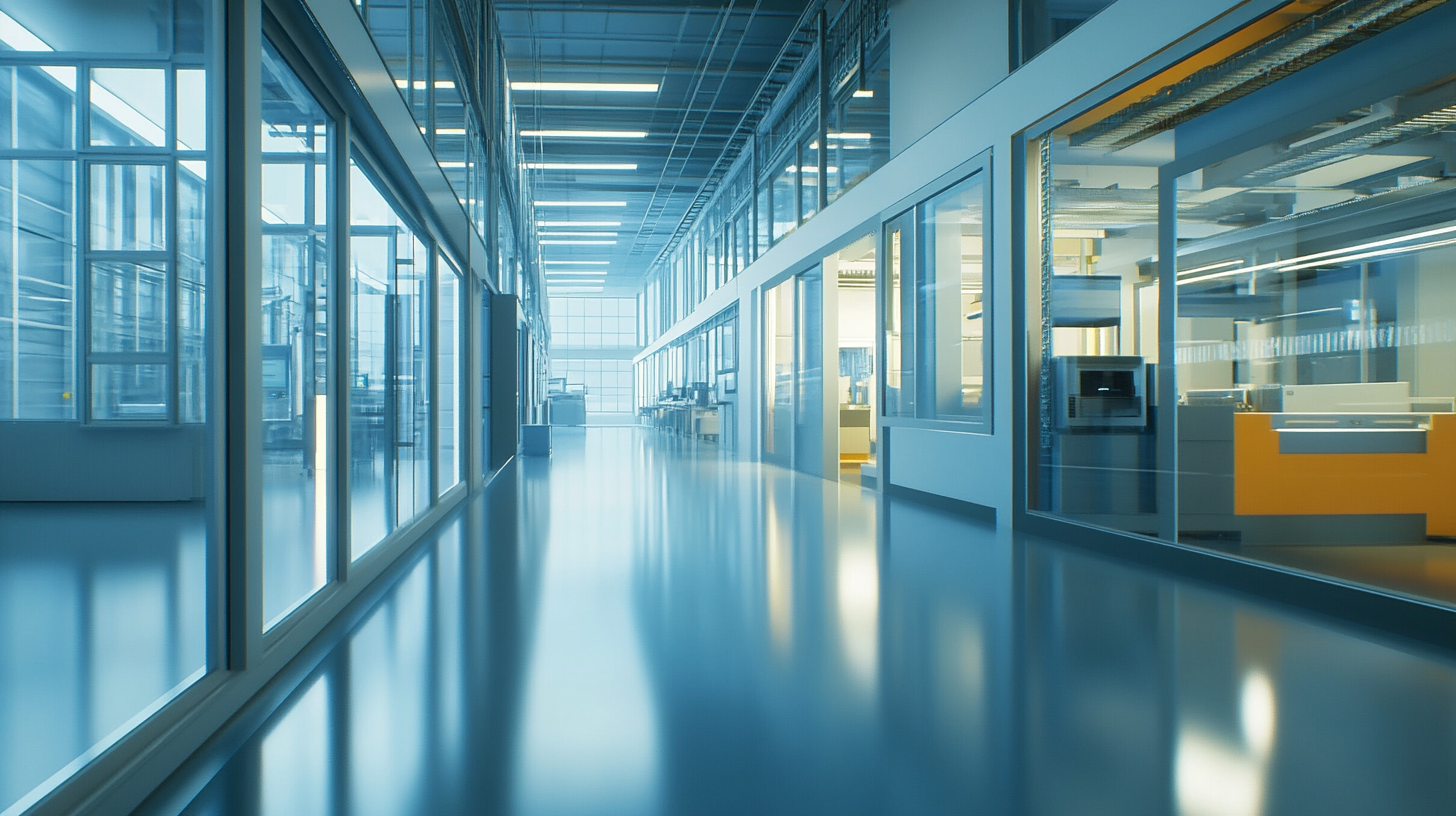
Impact of Automation on Window Production Efficiency
In the realm of window manufacturing, the implementation of automation technologies has revolutionized production efficiency. A report by the National Association of Manufacturers indicates that companies leveraging automated systems can increase productivity by up to 30%. This marked improvement is largely attributed to the reduction of manual labor and the minimization of human error, which traditionally plagued production lines.
Moreover, the integration of advanced robotics and computer numerically controlled (CNC) machines offers manufacturers enhanced precision and speed. The 2022 Industry Automation Report highlights that CNC machining can produce intricate designs with a tolerance of ±0.001 inches, significantly advancing the quality of finished windows. This precision not only leads to higher customer satisfaction but also reduces waste material, contributing to both environmental sustainability and cost efficiency.
Furthermore, automation allows for more flexible and scalable production lines. According to a survey by the Association for Manufacturing Technology, 64% of manufacturers who adopted automation reported improved ability to respond to market demand fluctuations. As consumer preferences evolve, being able to rapidly adjust production schedules and product specifications becomes crucial for maintaining competitiveness in the market. The increased efficiency brought about by automation is undeniable, making it a necessary investment for window manufacturers aiming for long-term success.
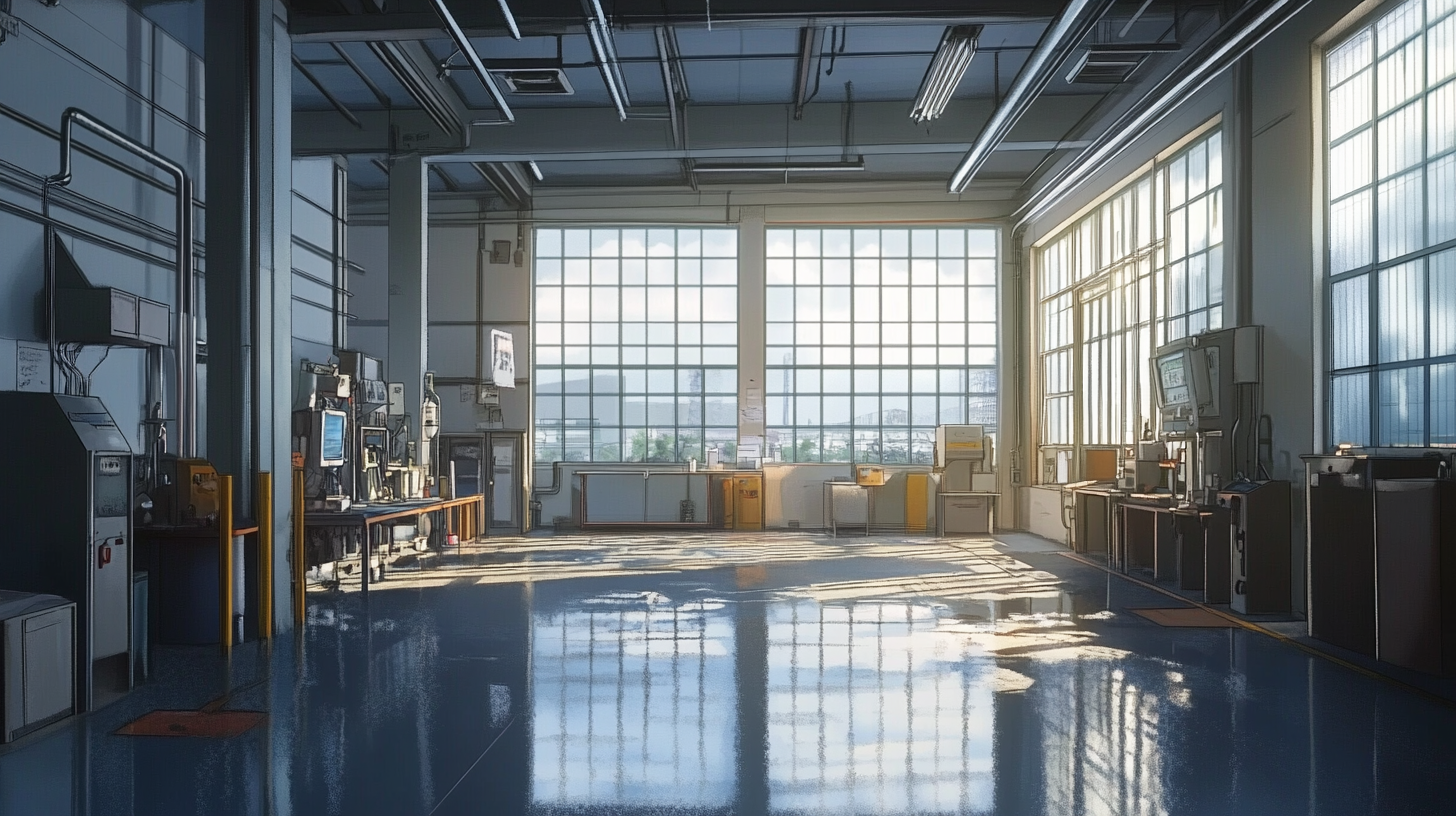
Analyzing Costs and Benefits of Different Window Fabrication Technologies
When considering the cost-effectiveness of window fabrication technologies, manufacturers must analyze both the initial investment and long-term operational efficiencies. Different types of equipment, such as CNC machines, glass tempering systems, and automated framing stations, offer varying degrees of precision and speed, which can significantly influence production timelines and labor costs. For instance, while CNC machines require a higher upfront investment, they can considerably reduce manual labor costs and minimize material waste through precise cutting and shaping.
Moreover, the benefits of advanced window fabrication technologies extend beyond mere cost savings. Innovations in energy-efficient window production not only cater to the growing demand for sustainable building materials but can also lead to tax incentives and stronger market positions. Benefits such as faster turnaround times and improved product quality also enhance customer satisfaction and open opportunities for premium pricing strategies. Therefore, assessing the balance of costs and benefits is crucial for manufacturers aiming to remain competitive in a rapidly evolving market.
Ultimately, determining the optimal production equipment requires a holistic evaluation of both financial implications and operational capabilities. By weighing the initial costs against the potential for increased efficiency and product quality, manufacturers can make informed decisions that align with their business goals and market demands. As the window fabrication industry continues to innovate, those who analyze and invest wisely in the right technologies will be positioned to thrive in an increasingly competitive landscape.
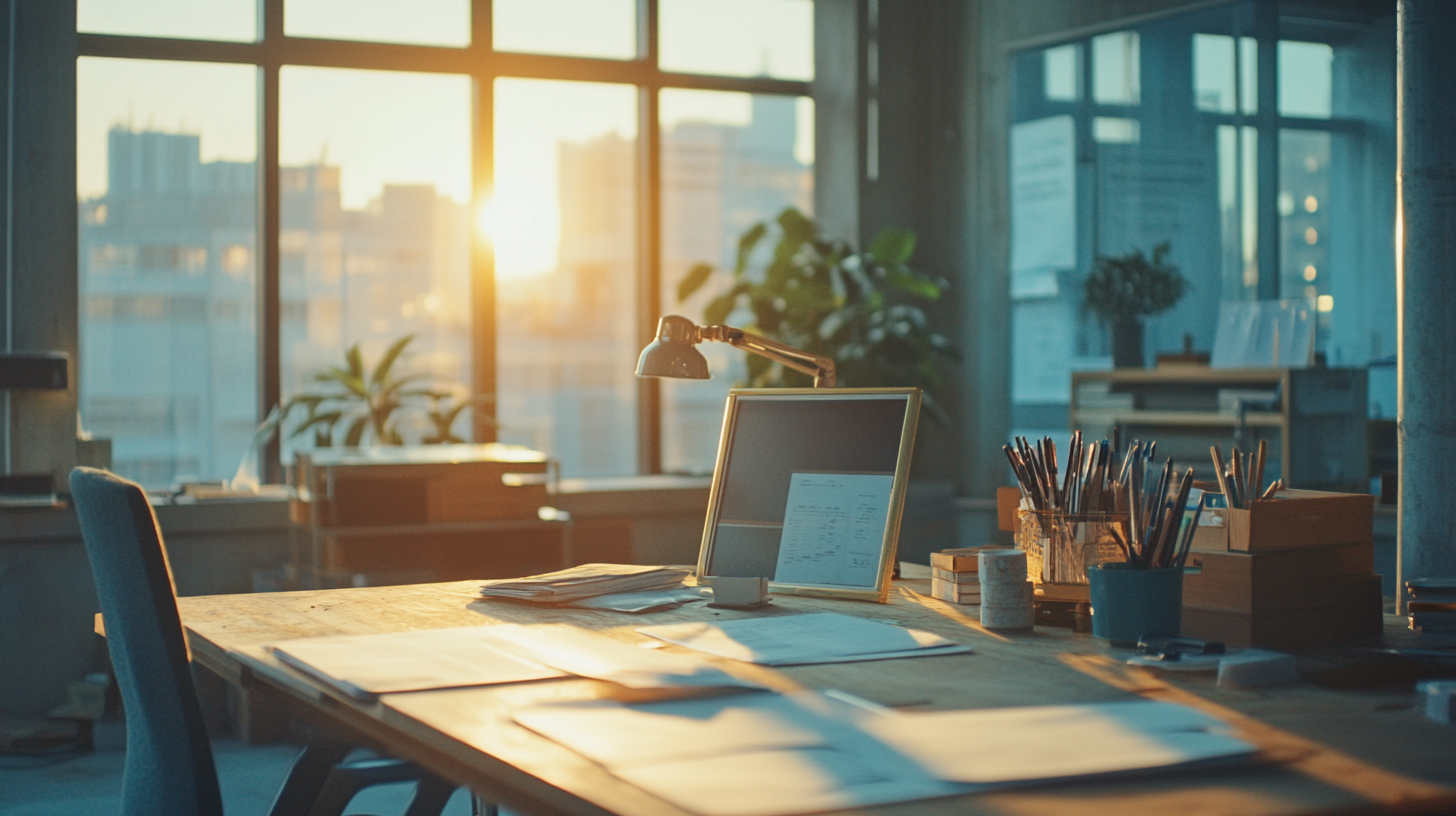
Latest Innovations in Window Manufacturing: Trends and Data
In recent years, the window manufacturing industry has witnessed exciting innovations that not only enhance production efficiency but also cater to evolving consumer demands. According to a report by Smithers Pira, the global window and door market is projected to reach $293 billion by 2027, with a compound annual growth rate (CAGR) of 3.5%. This growth is driven by advancements in manufacturing technologies, which streamline processes and reduce waste.
One of the notable trends is the adoption of automated machinery, which has increased productivity by up to 25%, as reported by the Window & Door Manufacturers Association (WDMA). The integration of robotics in window production allows for precision cutting and assembly, significantly minimizing errors and rework. Furthermore, the implementation of Industry 4.0 technologies, including data analytics and IoT, has enabled manufacturers to optimize their production lines through real-time monitoring and predictive maintenance. A study from McKinsey highlights that companies leveraging these technologies can reduce operational costs by 20-30%, proving that innovation in equipment is crucial for maintaining competitive advantage.
In addition to automation, sustainable manufacturing practices are reshaping the sector. The latest data from the U.S. Department of Energy indicates that energy-efficient window options, such as those incorporating low-emissivity (Low-E) coatings, are consistently gaining traction among consumers. This not only aligns with regulatory measures aimed at reducing carbon footprints but also offers manufacturers opportunities to differentiate their products in a crowded market. As the window manufacturing landscape continues to evolve, staying abreast of these trends and innovations will be key to achieving optimal production efficiency and meeting customer expectations.
Key Performance Indicators for Assessing Equipment Efficiency in Window Production
In today’s competitive window manufacturing industry, maximizing production efficiency is paramount. Key performance indicators (KPIs) serve as essential metrics for assessing the effectiveness of various types of window manufacturing equipment. These indicators can significantly influence decision-making processes, enabling manufacturers to identify bottlenecks and areas for improvement in their production lines.
One of the primary KPIs to consider is the overall equipment effectiveness (OEE), which measures the percentage of manufacturing time that is truly productive. This metric encompasses three critical factors: availability, performance, and quality. By analyzing OEE, manufacturers can pinpoint specific issues such as equipment downtime, speed loss, and defects, allowing for targeted strategies that enhance productivity.
Another critical performance indicator is the cycle time, or the total time taken to complete a single production cycle. Shortening cycle time not only improves output but also allows for greater responsiveness to market demands. By evaluating cycle time across different manufacturing processes and equipment types, manufacturers can streamline operations and reduce excess lead times. Implementing real-time monitoring systems can further aid in tracking these KPIs, empowering manufacturers to make swift adjustments and optimize their workflow continuously.
Additionally, energy consumption is a vital KPI, especially in an era where sustainability is increasingly prioritized. By assessing the energy efficiency of window manufacturing equipment, manufacturers can reduce costs and minimize their environmental impact. Understanding and benchmarking these KPIs allows businesses to foster a culture of continuous improvement, ensuring they remain competitive in a rapidly evolving market.