Maximizing Efficiency with PVC Window Welding Machines Through Reduced Maintenance Costs and Enhanced Support
In the modern manufacturing sky , efficiency and cost-effectiveness are the key consideration factors in PVC windows manufacturing. The PVC window welding machine plays a transformative role in this scenario; with its advanced technology, the welding process can be efficiently performed with low operational costs. As the trend of high-quality window solutions is gaining momentum, manufacturers are trying to find modern ways to optimize their processes to be competitive in a mercurial marketplace. This blog will emphasize how the adoption of state-of-the-art PVC window welding machines can enhance production efficiencies, causing a considerable cut in maintenance costs.
Maintenance and support greatly determine the lifespan and functionality of such machines. Companies that invest in good-quality PVC window welding machines will enjoy better support, which in turn helps keep the machines running efficiently. Proper maintenance with expert advice will extend the life of these machines and consequently will double the profitability. The blog will outline ways to increase efficiency by cutting down on maintenance and promoting better support systems for the sustainable manufacture of PVC windows.
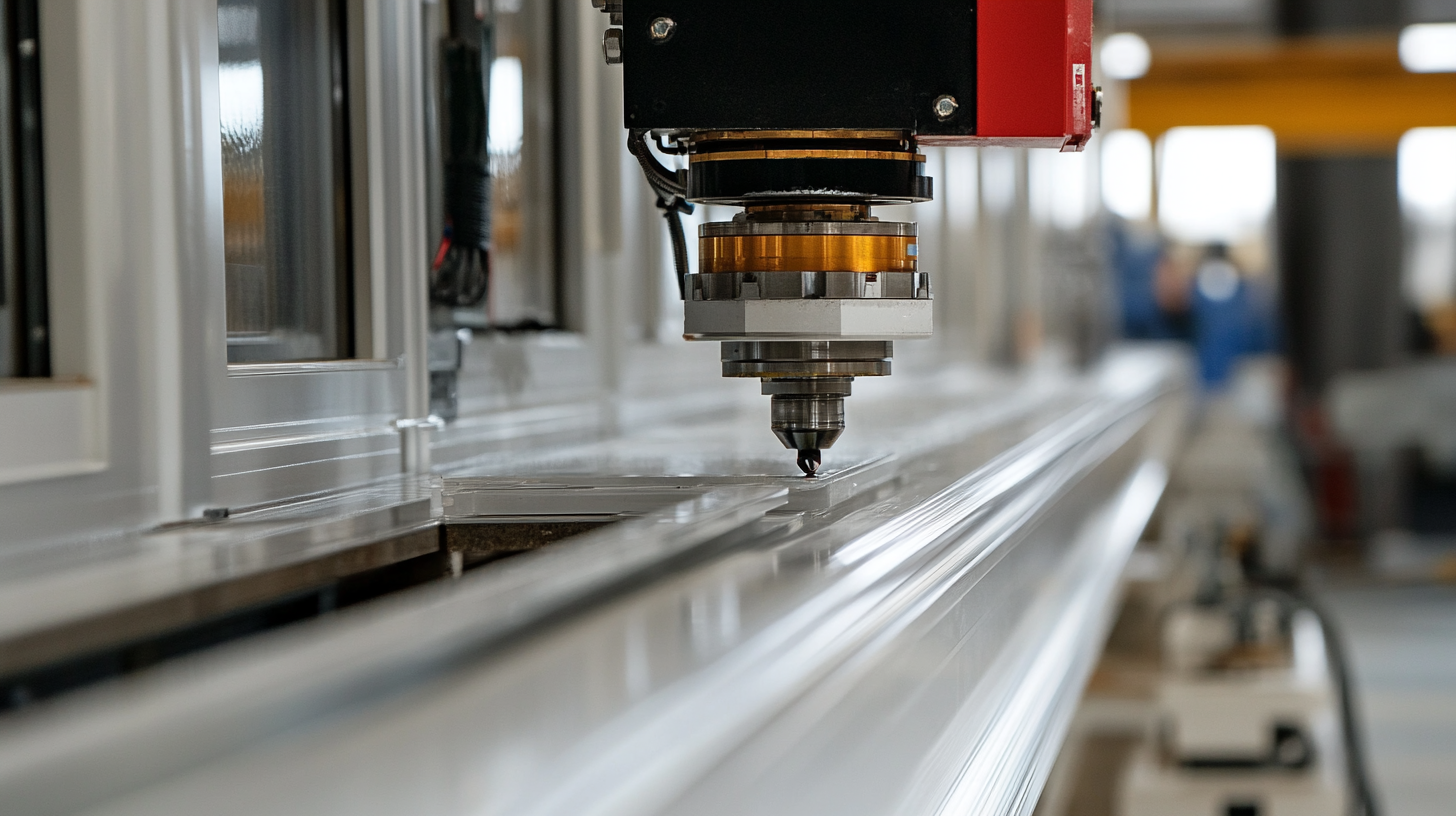
Understanding the Importance of Maintenance in PVC Window Welding Machines
Understanding Importance of Maintenance in PVC Window Welding Machines The days have gone when we only attributed productivity to the manufacturing sector in relation to human input. Usually, the roles played by manufacturing equipment in production are vital to the realization of overall productivity. For instance, the welding machine for PVC windows is one exception. As seen in a recent report by the European Window and Door Manufacturers Association (EWDA), it has been found out that "regular maintenance" according to this report could extend the life of welding machines by as much as 40 percent. Evidently, this pinpoints not only a necessity for maintenance but also its ROI which can, therefore, allow manufacturers to use their machines to the fullest without replacing them costs. There are many benefits of scheduled maintenance, such as prolonging the life of equipment and reducing machine down time significantly. A study published by the International Institute of Welding states that 30% less machine failure occurs in companies practicing proactive maintenance. This translates fewer raw materials to production, ultimately increasing the outputs. Regular units and parts checkups, replacement, and updates on software help ensure that machines operate at their more excellent performance, therefore accurate welding and reduced scrap rates. Enhancement of support from manufacturers streamlines the maintenance process. A more recent survey has shown that 65% of manufacturing professionals said immediate technical support translates into better performance in terms of operations. Providing substantial training and materials, companies would be better able to do the maintenance themselves, thus reducing costs. Emphasis on immediate support not only increases efficiency of operation, but also ingrains an improving mentality among the human resource. These go a long way to maximizing the output and reliability of PVC window welding machines.
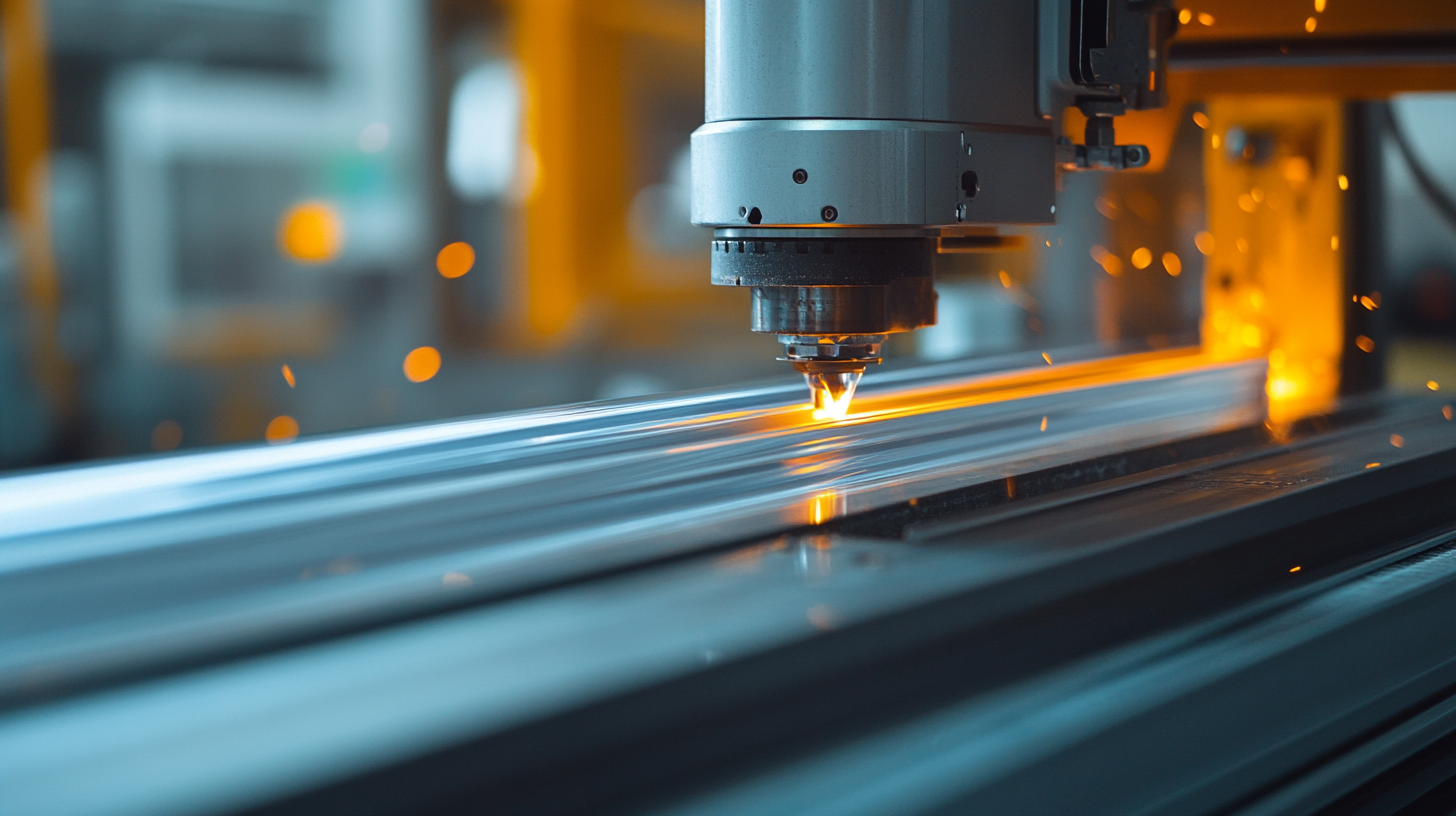
Strategies for Reducing Maintenance Costs in Welding Operations
In the tough and challenging world of manufacturing, particularly in the automotive segment, it is wise to say that welding maintenance costs will be low. A good number of approaches such as up-to-date technologies coupled with better optimization have given great reduction in downtime and operational cost. A specific approach in maintaining the welding shop would help a great deal for companies to improve their overall efficiency.
Predictive maintenance is one-of such strategy implemented by a well reputed company. It has made real-time condition monitoring for the assets by predictive algorithms using high-end sensors and big data analytics for the less failure requirement before failure of machines. This results in a lower percentage of unplanned machine maintenance events, cost reduction, and more productivity. Other changes to consider are staff training. But very importantly, it is vital to have the operators trained in best-use practices with a machine, as it could minimize unneeded wear and tear, which would further reduce maintenance expenses.
In addition, the assets will be worth the price paid for them in the long run. The more inexpensive, albeit initially costly, high-end welding equipment pays significantly more dividends in terms of reliability and efficiency, having overall lower lifetime costs. Once this is tied to a powerful support structure like easy access to tech support and available spare parts, the business will dramatically improve in its capacities. Companies, therefore, create the perfect business sense for all their activities by adopting competitive measures for them to be ahead in the extremely fast-growing and aggressively shifting sector.
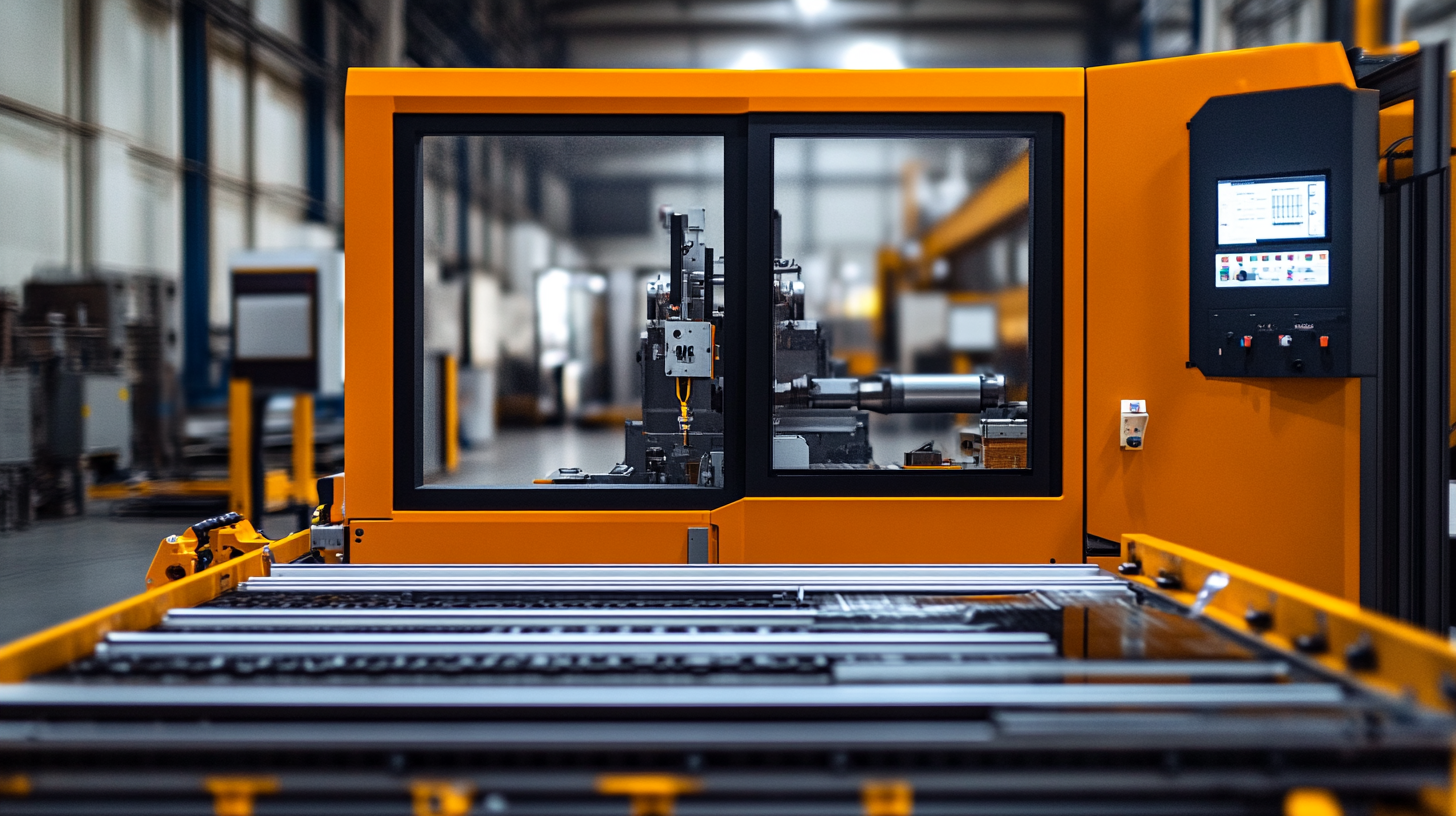
Enhancing Technical Support for Optimal Machine Performance
Excellent machine performance optimization can indeed mean the very lease for manufacturers in a competitive environment and nowhere is its importance more urgent than in the domain of PVC Window Welding Machines. Technical support is, therefore, of particular importance. Technical support that enables the machines to always work without interruptions contributes greatly to the company's productivity as downtime is a problem no longer witnessed. Training sessions and workshops for operators go a long way in giving them an understanding of their equipment—such understanding is essential so that an operator can perform routine maintenance tasks and catch any problem in time before it gets serious.
Another pointer is that a good yield can be reaped if manufacturers invest in their technical group, providing them with full knowledge of the latest in welding capabilities. There should be a very rapid technology provision that is used for bettering their welding systems-troubleshooting of complex issues, guidelines, and some best-practice suggestions for the optimum settings of the welding systems completely much more enhanced. These supportive engagements may contribute in minimizing the time spent in resolution of any technical issues, eventually pondering uninterrupted service time for production.
Mending any technical issue is much less valuable when technical support, in the true sense, is perceived simply as the main vehicle for building everlasting dream worlds for learning models and performance improvement. In other words, the better operators can feel their way through the day-to-day running and care of machinery, the better for production quality and general economics. The willingness to enhance a genuine relationship will thus pay instant dividends for those producers and all others who venture towards taking the road where they are presently positioned in a fast changing environment.
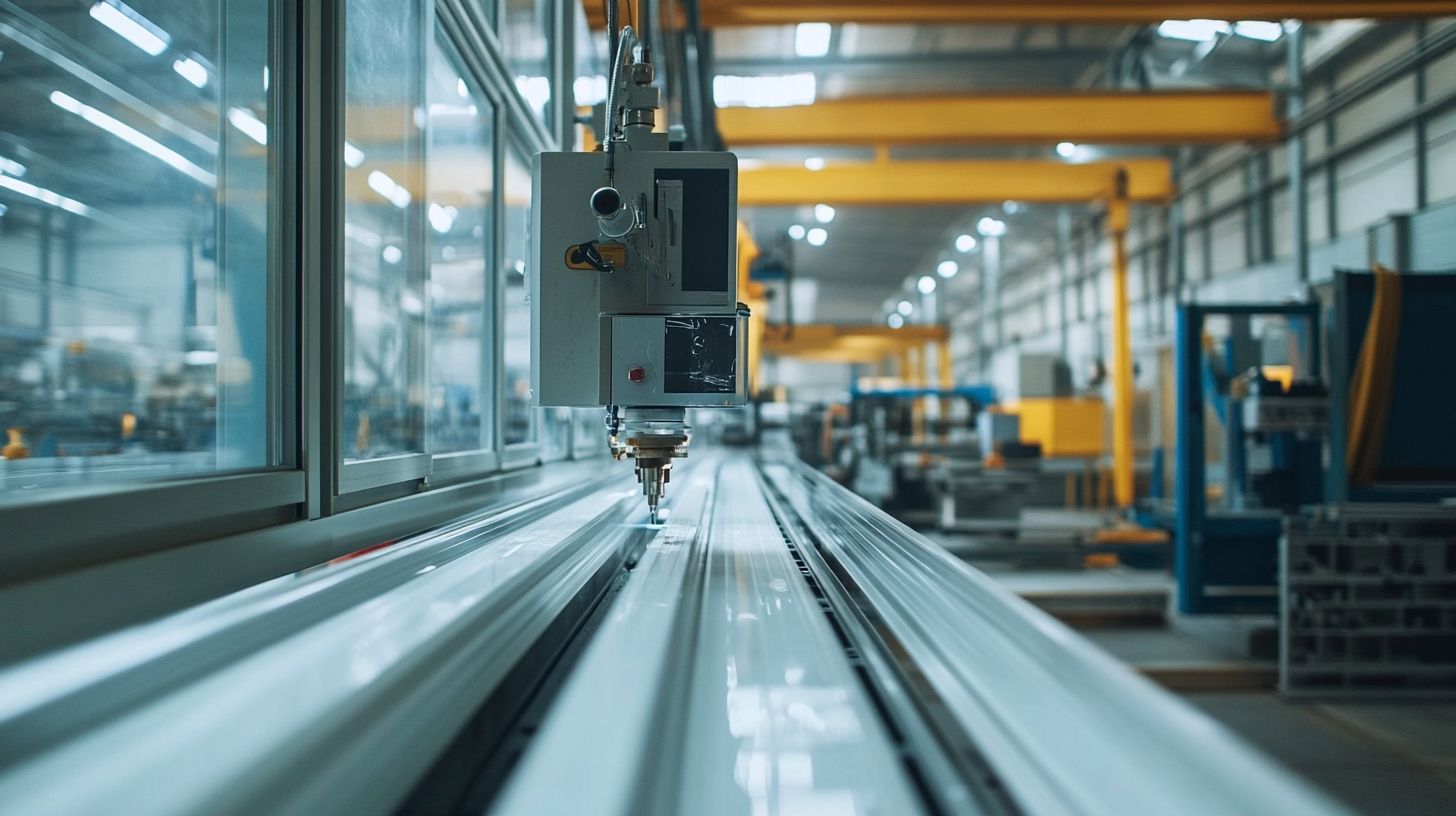
Investing in Employee Training for Better Machine Utilization
Employee training is highly important in maximizing the efficiency of PVC window welding machines. These robots certainly increase productivity significantly by employing well-trained staff. Without training, employees won't be able to use the machines fully and often run into inefficient operations as well as increased maintenance costs. A good training program would fully prepare the workers for various welding processes, troubleshooting minor issues, and performing routine maintenance, resulting eventually in longer machine life.
They will also look out for potential problems to avoid that and even take action before it occurs, thus helping to reduce downtime. Training should not be confined to single events but rather continuous and updated in time with the passage of time because that will ensure employees are up-to-date with modernization and state-of-the-art practice. Practical workshops and simulation exercises would be fundamental experiences for improvement, giving employees hands-on exposure besides theoretical understanding. When workers feel they are competent, it encourages them to put ideas forward because this creates an innovative organizational culture.
Prioritizing employee growth has found businesses creating an accomplished workforce in machine use. That much saw less spending on maintenance about processes and enhanced efficiency in production. Improved skills by employees mean improved quality products and ultimately improved customer satisfaction, which are determinants for competitiveness in the market. The training will indeed pay back and add to the overall success of the organization.
Innovative Features to Look for in Modern PVC Welding Machines
Every time this world is changing, so is PVC window welding machine. Modern innovations seem to play an important role in efficiency and maintenance cost savings. Though all brands want to have new features, the most important one manufacturers should be considering is whether the tool helps weld joints more easily and supports the user in an efficient manner. Optimum for operator errors, thus contributing to much higher product quality precision and uniformity, the manufactured products will enjoy these benefits.
From the latest market analysis, it states that Rigid PVC Windows and Door markets will flourish with an increase in demand for strong and architecturally valuable building materials. The reports comment on the fact that PVC technology states improved resistance to environmental stressors, resulting in an increased lifespan and maintenance-free lifecycle. Self-cleaning surface, built-in monitoring systems, and similar techniques would supplement productivity even further and minimize long-term costs.
In fact, by green means modern PVC welding machines can be made. For example, being part of a group that will make PVC waste upcycle into feedstock systems gives manufacturers an edge of novelty and environmental responsibility. These techniques, as they progress, will not only ensure an efficient production process but also mark the way for a sustainable future for the entire PVC industry.