Unlocking Efficiency in Aluminium Door Window Manufacturing Machines for Global Buyers
In the rapidly evolving landscape of construction and architecture, the demand for high-quality aluminium door and window solutions has surged significantly. According to a recent report by MarketsandMarkets, the global aluminium windows and doors market is projected to reach $126.7 billion by 2025, growing at a compound annual growth rate (CAGR) of 5.9% from 2020. This sizeable growth underscores the necessity for manufacturers to invest in advanced technology, specifically in Aluminium Door Window Manufacturing Machines, which are pivotal for enhancing production efficiency, optimizing material usage, and reducing labor costs.
As global buyers increasingly prioritize sustainable and energy-efficient building materials, the efficiency of manufacturing processes becomes paramount. The right Aluminium Door Window Manufacturing Machine can drastically elevate production rates while maintaining precision and quality. With technological innovations paving the way for automation and smarter manufacturing practices, companies that leverage these advancements can not only fulfil market demands but also gain a competitive edge. Delving into the latest developments and best practices in aluminium door and window manufacturing will unlock new efficiencies and enhance profitability for manufacturers worldwide.
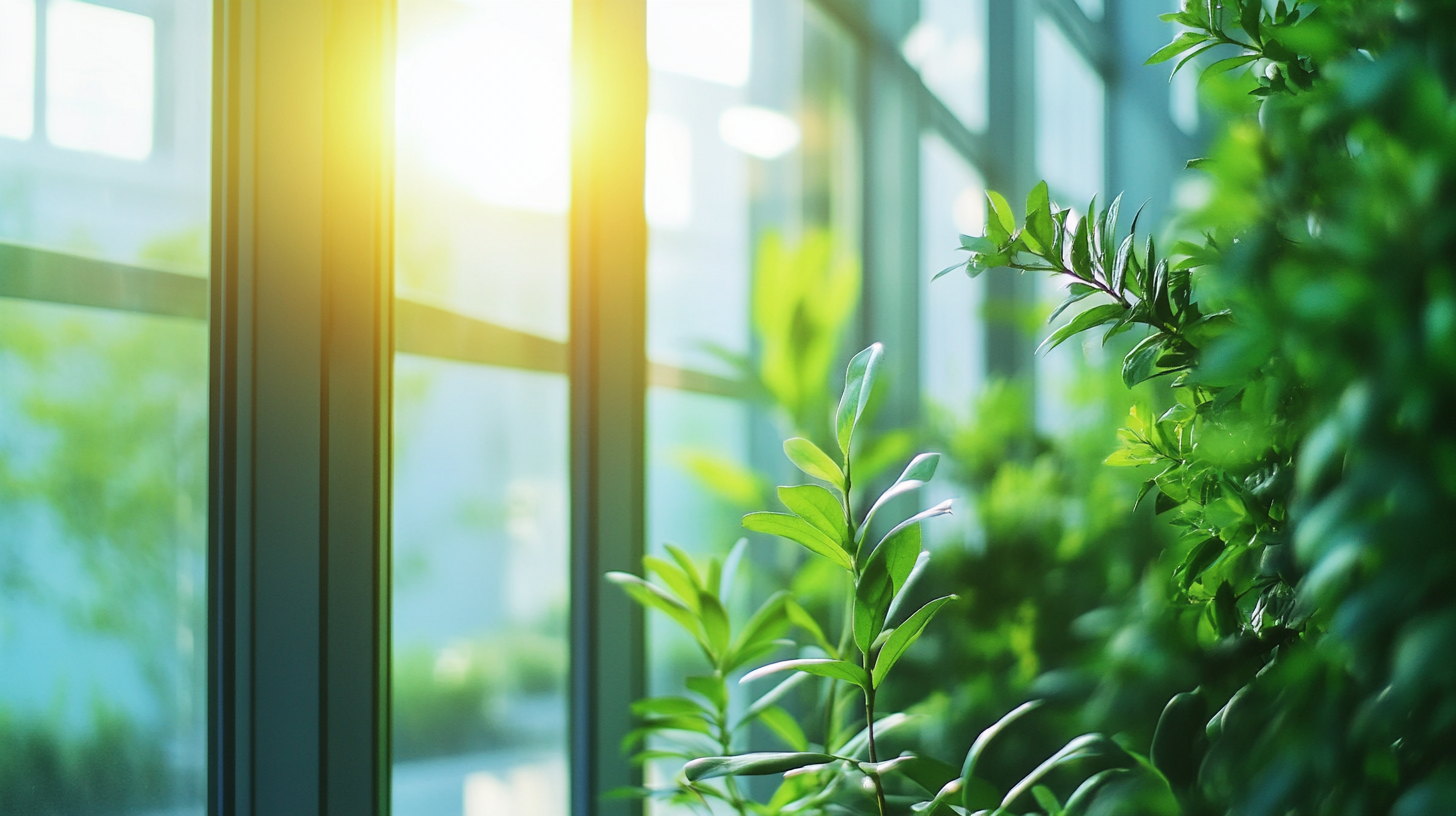
Innovative Technologies Reshaping Aluminium Door Window Manufacturing Efficiency
In the dynamic landscape of the aluminium door and window manufacturing industry, innovative technologies play a crucial role in enhancing efficiency and productivity. Recent projections indicate that the European doors and windows market, valued at USD 58.75 billion in 2023, is poised for significant growth, expected to reach USD 71.05 billion by 2029, representing a compound annual growth rate (CAGR) of 3.22%. This rapid expansion underscores the need for manufacturers to adopt cutting-edge technologies that streamline production processes and reduce costs. One of the key advancements includes automation technologies that facilitate quicker and more precise manufacturing, allowing companies to meet increasing market demands effectively. Incorporating robotics and AI-driven systems not only accelerates production but also minimizes material waste, ultimately leading to increased sustainability—a critical factor in attracting global buyers who are increasingly environmentally conscious. Moreover, the integration of smart manufacturing solutions, such as IoT (Internet of Things)-enabled machinery, enhances operational visibility and control. This interconnectedness allows manufacturers to monitor processes in real-time, identify bottlenecks, and optimize resource allocation. As the industry faces pressure to innovate and adapt, embracing these technologies will be vital for companies aiming to maintain a competitive edge in a lucrative market that shows promising growth potential.
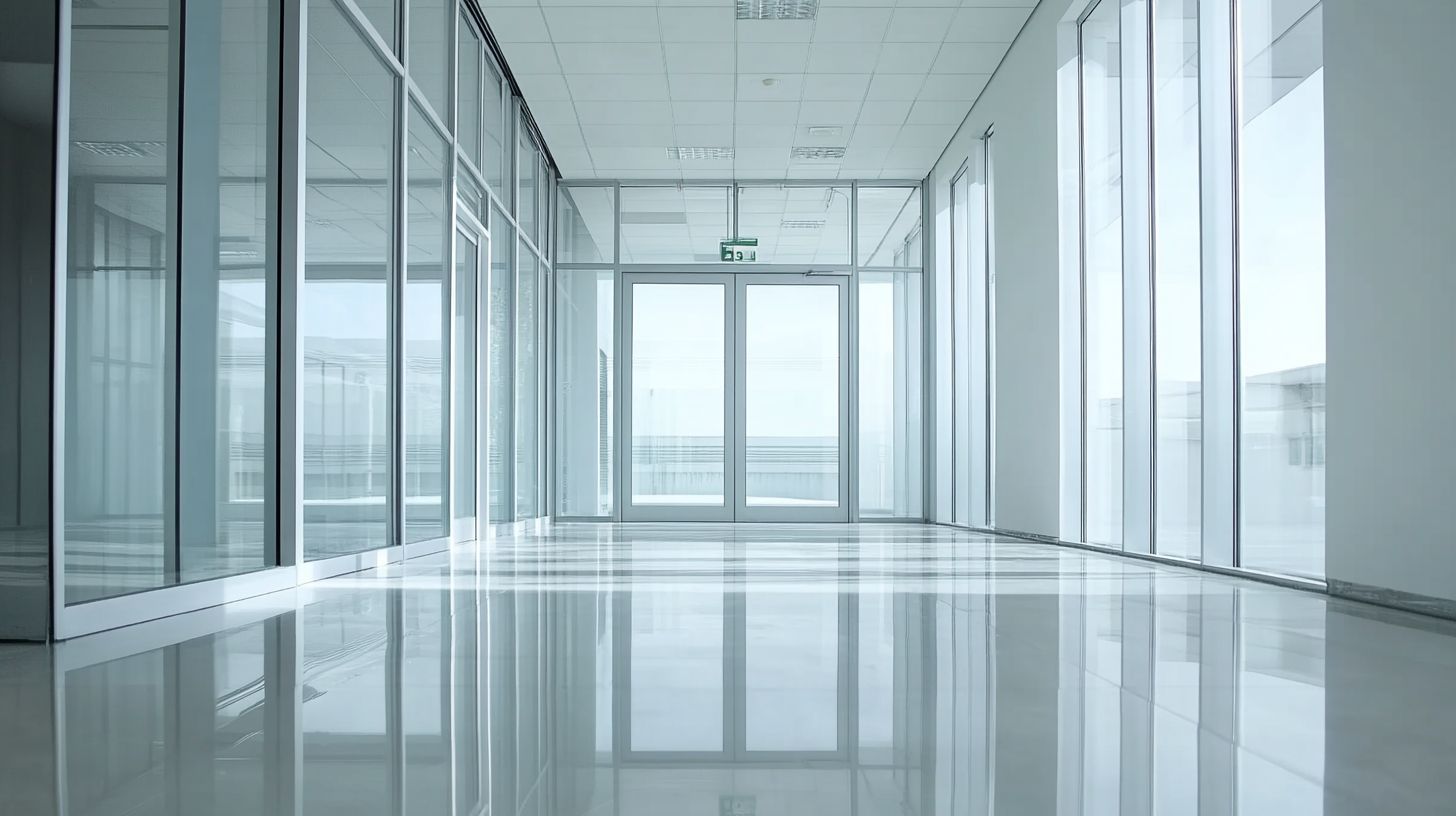
Key Benefits of Automation in Aluminium Manufacturing Processes
The aluminum door and window manufacturing sector is increasingly embracing automation to enhance productivity and efficiency. According to a report by MarketsandMarkets, the global market for automated manufacturing equipment is expected to grow from $191 billion in 2020 to $284 billion by 2026, driven by the need for improved operational efficiency and reduced labor costs. Automation not only streamlines processes but also minimizes waste and enhances accuracy, which are critical factors in maintaining competitiveness in a fast-evolving market.
One of the significant benefits of automation in aluminum manufacturing processes is the reduction in manual errors. A study published by the American Society of Mechanical Engineers highlights that automated systems can reduce error rates by as much as 50%. This improvement translates to higher product quality and lower rework costs, which are essential for businesses that aim to meet stringent global quality standards. Furthermore, automation allows for quicker turnaround times, enabling manufacturers to respond rapidly to market demands without compromising on quality.
Additionally, the deployment of advanced technologies such as AI and machine learning in aluminum manufacturing can optimize production schedules and resource allocation. According to a report by McKinsey & Company, companies that have integrated automation and AI have seen productivity increases of 15% to 30%. This level of efficiency not only results in cost savings but also positions manufacturers to scale operations as needed, thus fostering a more agile supply chain capable of adapting to global trends.
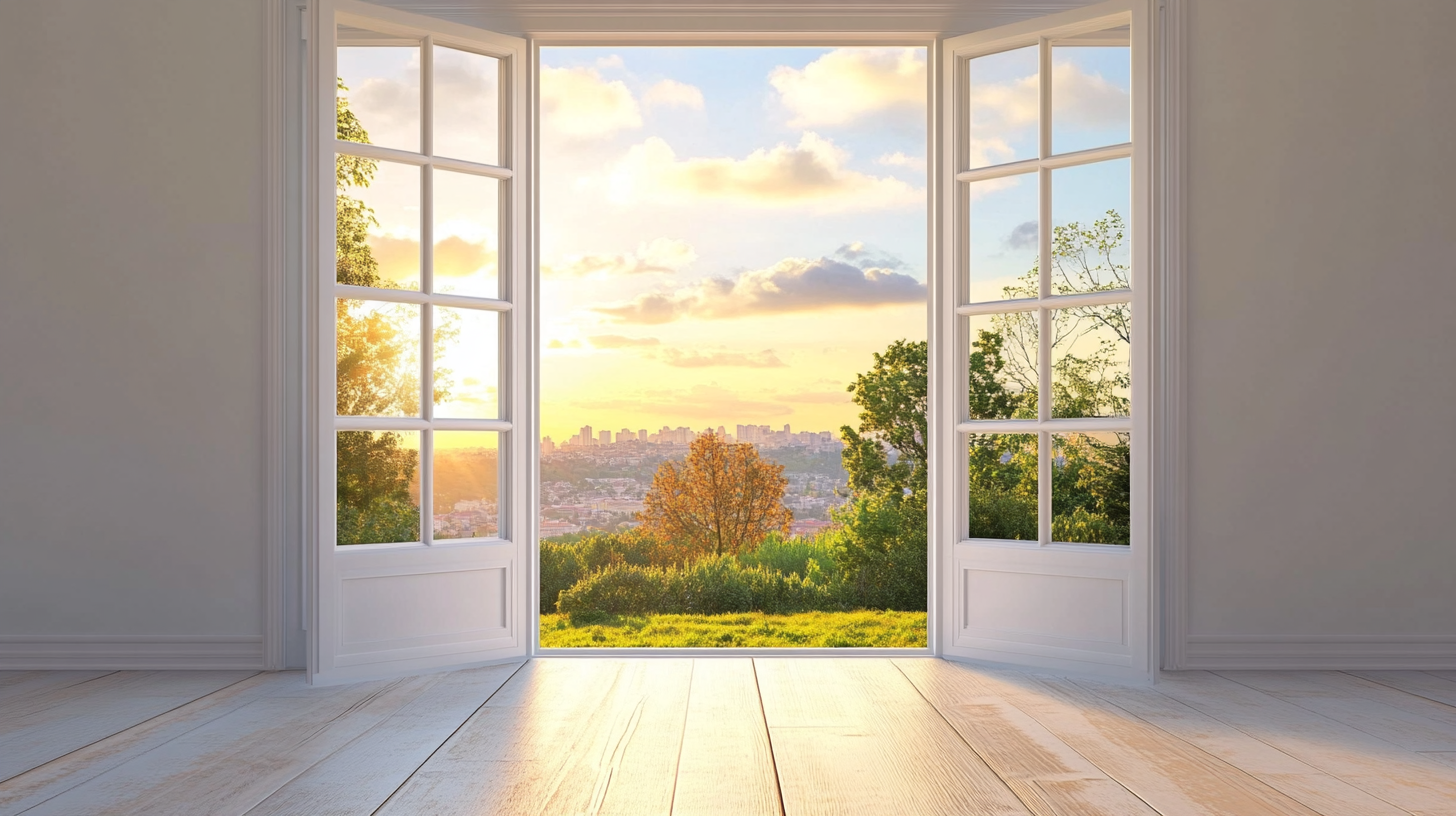
Market Trends: Demand for Sustainable Aluminium Solutions in Global Markets
As the global market shifts towards sustainability, the demand for eco-friendly aluminium solutions in door and window manufacturing is on the rise. Data from the World Aluminium Association indicates that the aluminium industry is expected to grow by 3.3% annually through 2025, driven primarily by increasing interest in sustainable construction practices. This growth highlights a significant trend where manufacturers are focusing on the production of energy-efficient and recyclable aluminium products.
Moreover, the International Energy Agency (IEA) reports that buildings account for approximately 40% of global energy consumption, underscoring the importance of sustainable materials like aluminium in reducing environmental impact. The shift towards energy-efficient manufacturing processes also aligns with consumer preferences. Recent surveys indicate that over 70% of consumers prioritize sustainability when making purchasing decisions, further encouraging aluminium door and window manufacturers to innovate and adapt their production methods.
The adoption of advanced technologies, such as automation and smart manufacturing, is enhancing the efficiency of aluminium production while minimizing waste. A report by Grand View Research projects that the global aluminium extrusion market will reach $100 billion by 2025, bolstered by rising demand for high-performance aluminium framing systems in green buildings. This evolution not only meets the regulatory requirements but also aligns with broader goals of reducing carbon footprints and promoting responsible sourcing within the construction sector.
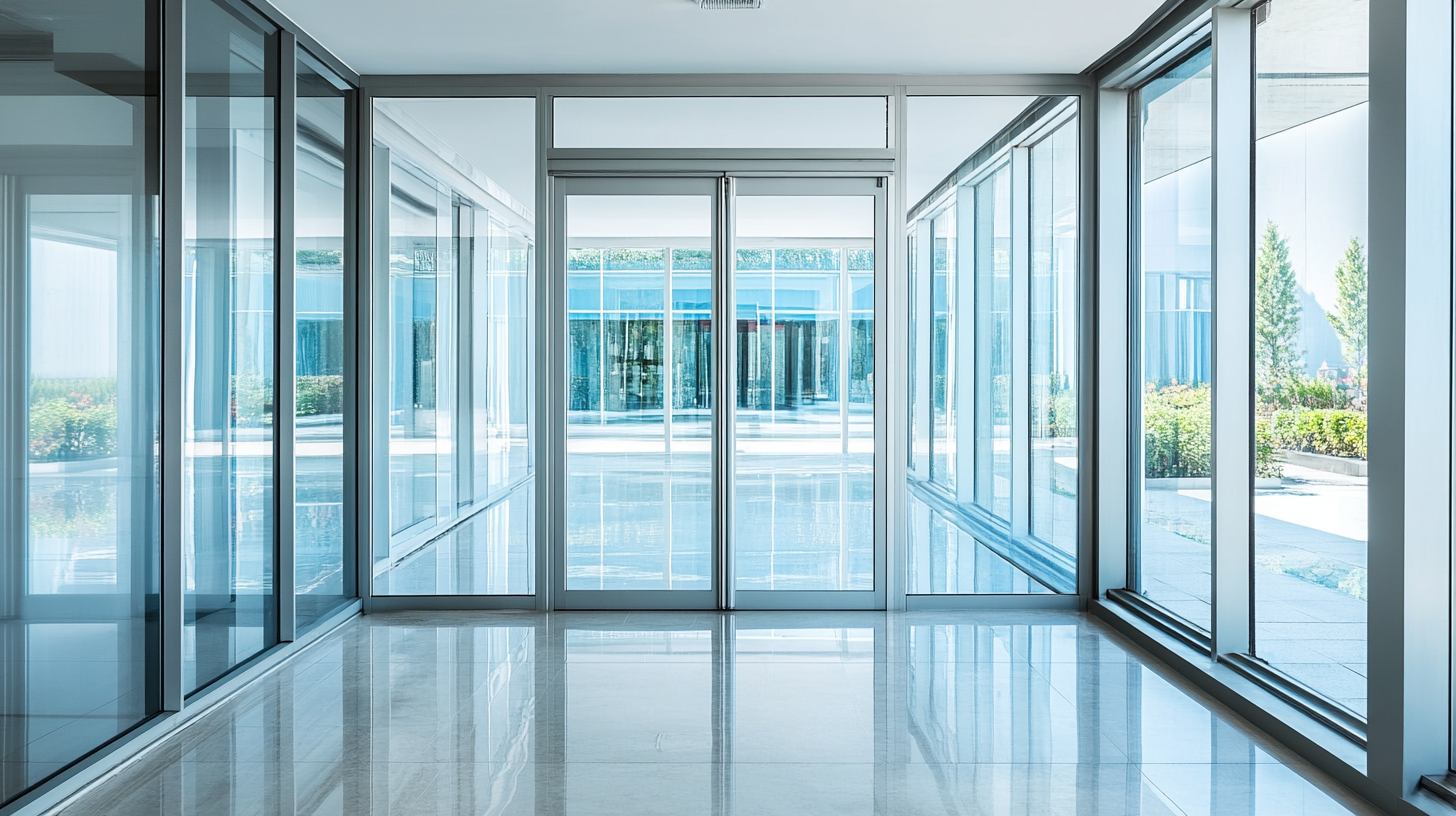
Cost Analysis: Long-term Savings with Advanced Manufacturing Machinery
In the competitive landscape of aluminium door and window manufacturing, advanced machinery plays a pivotal role in enhancing operational efficiency and driving down costs. When assessing the long-term savings of investing in high-tech manufacturing machines, several factors come into focus. These include reduced labor costs, minimized material waste, and improved production speed, all of which contribute to a healthier bottom line.
Advanced manufacturing machinery is designed to optimize workflows and streamline production processes. For instance, automated systems can significantly reduce the time required for tasks such as cutting, welding, and assembly. This not only diminishes the need for manual labor but also allows companies to allocate resources more effectively, driving productivity. Over time, the initial investment in these sophisticated machines is often offset by the savings realized through increased output and efficiency.
Moreover, modern manufacturing technologies come equipped with precision engineering capabilities that lessen material waste. Traditional machinery may incur higher scrap rates due to inaccuracies in production, leading to added costs for raw materials. In contrast, advanced machines utilize cutting-edge software and sensors to ensure optimal performance, allowing for precise cuts and assembly that drastically decrease wastage. The cumulative effect of these efficiencies can translate to significant cost benefits over the lifespan of the machinery, reinforcing the argument for global buyers to embrace these innovations in their manufacturing processes.
Enhancing Quality Control in Aluminium Production through Precision Engineering
In the realm of aluminium door and window manufacturing, precision engineering plays a pivotal role in enhancing quality control. As global buyers increasingly demand higher standards, manufacturers are turning to advanced technologies to ensure that every product meets rigorous quality specifications. The integration of machine vision systems, for instance, allows for real-time quality inspections, effectively detecting any defects in casting aluminium parts, such as filings and holes. This not only streamlines the production process but also significantly reduces waste, ensuring that only the highest quality products reach the market.
Moreover, the collaboration between industries is fostering innovation in aluminium production. A recent trend has seen manufacturing engineers drawing insights from the medical imaging sector, thereby enhancing quality control processes. The adoption of best practices across these fields is crucial to developing more reliable and efficient manufacturing systems. The Memorandum of Understanding (MoU) signed by Taural India with the Maharashtra Government exemplifies this initiative, as it aims to promote industrial development in Tier II regions, thereby expanding local capabilities and improving quality standards across the board.
As manufacturers continue to invest in precision engineering and advanced inspection technologies, the future of aluminium door and window production looks promising. With enhanced quality control mechanisms in place, global buyers can trust that they are receiving not only innovative designs but also products that adhere to the highest standards of excellence.