Unlocking Efficiency in Aluminium Window Manufacturing with Advanced Fabrication Machines
The aluminium window manufacturing industry has experienced significant growth, driven by the increasing demand for energy-efficient and sustainable building solutions. According to a report by Smithers Pira, the global market for aluminium windows is projected to reach USD 100 billion by 2025, with a compound annual growth rate (CAGR) of 4.5% from 2020 to 2025. This growth is largely attributed to the rising popularity of aluminium as a viable alternative to traditional materials, thanks to its durability, lightweight properties, and recyclability. As the industry evolves, manufacturers are seeking advanced technologies to streamline their processes, enhance productivity, and maintain competitive advantage.
One of the key innovations in this arena is the implementation of advanced Aluminium Window Fabrication Machines. These machines not only improve efficiency by reducing production times and waste but also enable manufacturers to meet stringent quality standards and customer demands for customization. A recent industry survey by MarketsandMarkets indicates that 70% of manufacturers are now investing in automation and state-of-the-art fabrication technologies to boost their operational capabilities. As we delve deeper into the potential of these machines, we will explore how they are transforming the landscape of aluminium window manufacturing, ultimately leading to better quality products and enhanced operational efficiency.
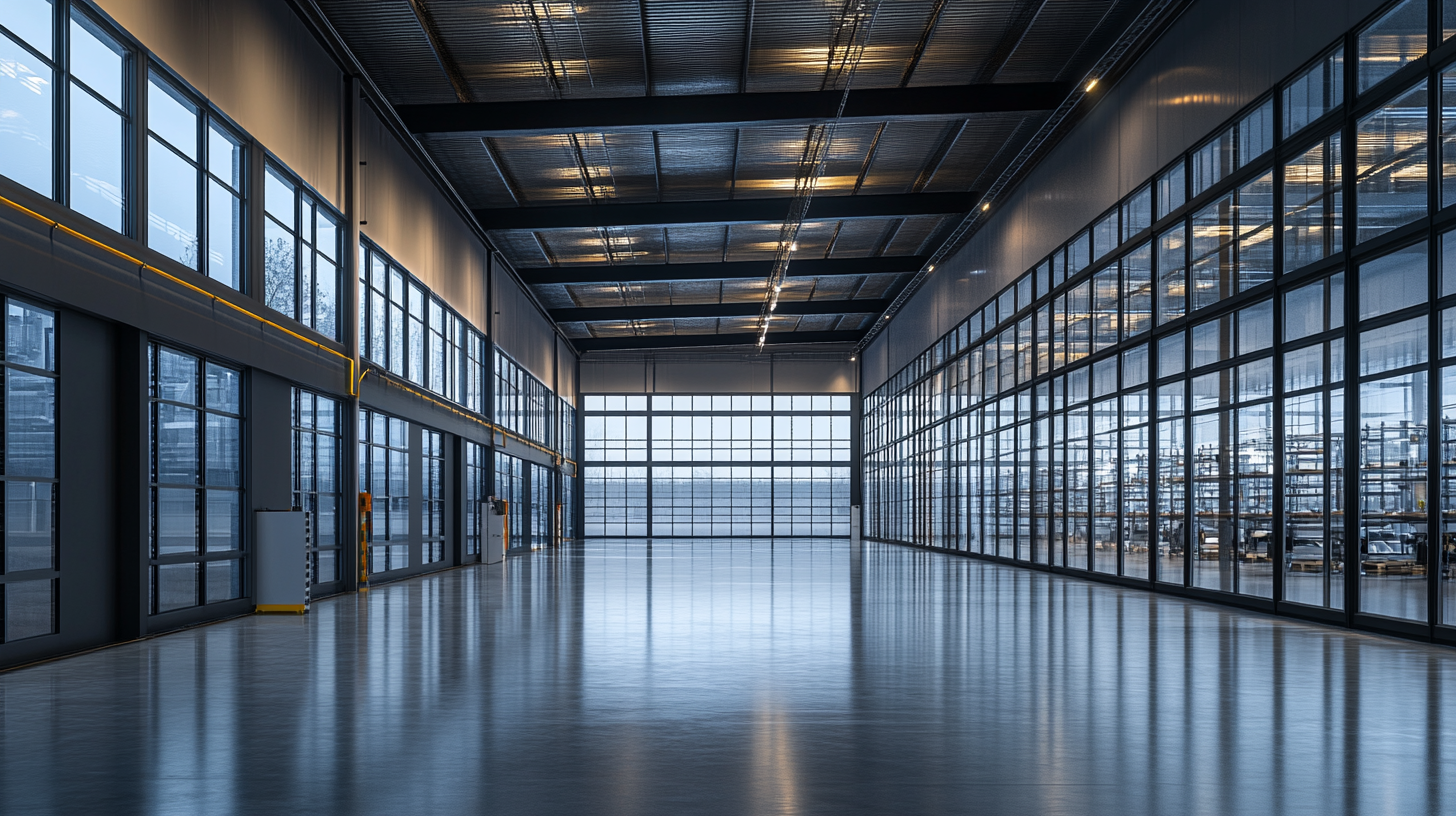
The Shift towards Automation in Aluminium Window Manufacturing
The shift towards automation in aluminium window manufacturing is revolutionizing the industry, with advanced fabrication machines playing a critical role. Companies are increasingly recognizing the need to streamline operations, which is evident in recent trends where high-speed machinery is pivotal for expediting production processes. However, it is essential to look beyond mere speed. Investments in automation must also prioritize precision and efficiency to ensure that the end products meet the highest quality standards. Recent developments highlight the urgency of this transition. For instance, engineers focused on automating the extrusion and assembly of components for storefronts and curtain walls are a clear indication of how automation can enhance the consistency and speed of production. Additionally, manufacturers like Joedan Manufacturing have installed automatic machining and sawing lines to boost their capabilities and output, demonstrating that automated solutions can significantly increase operational efficiency. Moreover, the integration of technologies such as RFID and real-time location systems in companies like Toro Aluminium is becoming commonplace. These innovations facilitate better tracking of materials and products through the manufacturing process, further optimizing production workflows. The introduction of AI and advanced automation systems is not just a trend but a necessary evolution, ensuring that aluminium window manufacturers can keep pace with increasing demand while maintaining superior quality and precision. This strategic pivot towards automation is set to define the future landscape of aluminium window manufacturing.
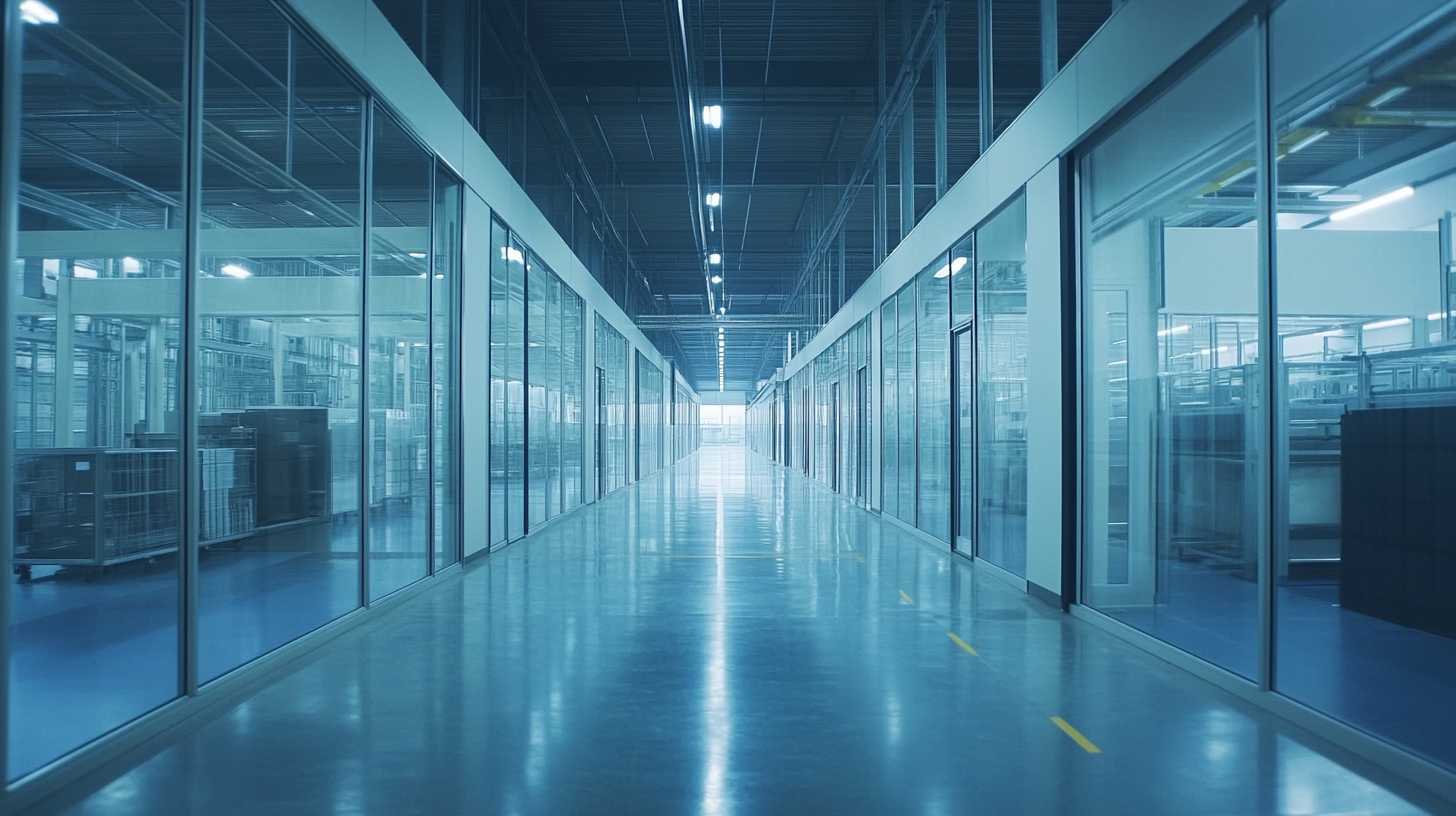
Impact of Advanced Fabrication Machines on Production Efficiency
In the competitive world of aluminium window manufacturing, the integration of advanced fabrication machines has proven to be a game changer in enhancing production efficiency. These machines incorporate cutting-edge technology that streamlines various manufacturing processes, significantly reducing operational time and labor costs. By automating tasks such as cutting, shaping, and assembling, manufacturers can achieve higher precision and consistency, which are crucial for meeting the rising demands of quality and customization in the market.
Moreover, advanced fabrication machines enable manufacturers to optimize resource usage, thereby minimizing waste. With better material handling capabilities and real-time data monitoring, these machines ensure that every piece of aluminium is utilized effectively. This not only lowers material costs but also aligns with sustainable manufacturing practices. Additionally, the speed at which these machines operate allows companies to increase their output, meeting tight deadlines and improving overall turnaround times.
The impact of these technologies extends beyond production efficiency; they also enhance the overall competitiveness of aluminium window manufacturers. By embracing innovation, companies can better adapt to market changes and customer preferences, ultimately leading to increased profitability. In today’s fast-paced environment, investing in advanced fabrication machines is not just an option but a necessity for those looking to thrive in the aluminium window industry.

Cost-Benefit Analysis of Upgrading to High-Tech Fabrication Equipment
The aluminium window manufacturing industry is witnessing a paradigm shift with the advent of advanced fabrication machines. These high-tech tools not only streamline production processes but also introduce a remarkable cost-benefit dynamic that manufacturers can no longer afford to overlook. According to a report by the International Aluminium Institute (IAI), upgrading to modern fabrication equipment can boost productivity by up to 30%, significantly lowering manufacturing costs over time.
A cost-benefit analysis reveals that while the initial investment in high-tech machines may be substantial, the long-term savings are compelling. For instance, a study by the European Aluminium Association highlighted that manufacturers who implemented automated fabrication technologies experienced a reduction in labor costs by as much as 25%, due to increased machine efficiency and reduced downtime. Additionally, these advanced machines often yield lower waste production—up to 15% less—leading to further material cost savings and a more sustainable manufacturing process.
Moreover, the integration of smart technologies, like Industry 4.0 capabilities, allows for real-time monitoring and optimization of the production line, enhancing overall operational efficiency. Reports indicate that such innovations can decrease cycle times by 20%, enabling manufacturers to respond more swiftly to changing market demands. As the aluminium window sector evolves, investing in advanced fabrication machines emerges as not just a strategic advantage, but a necessary step toward maintaining competitiveness in an increasingly demanding market.
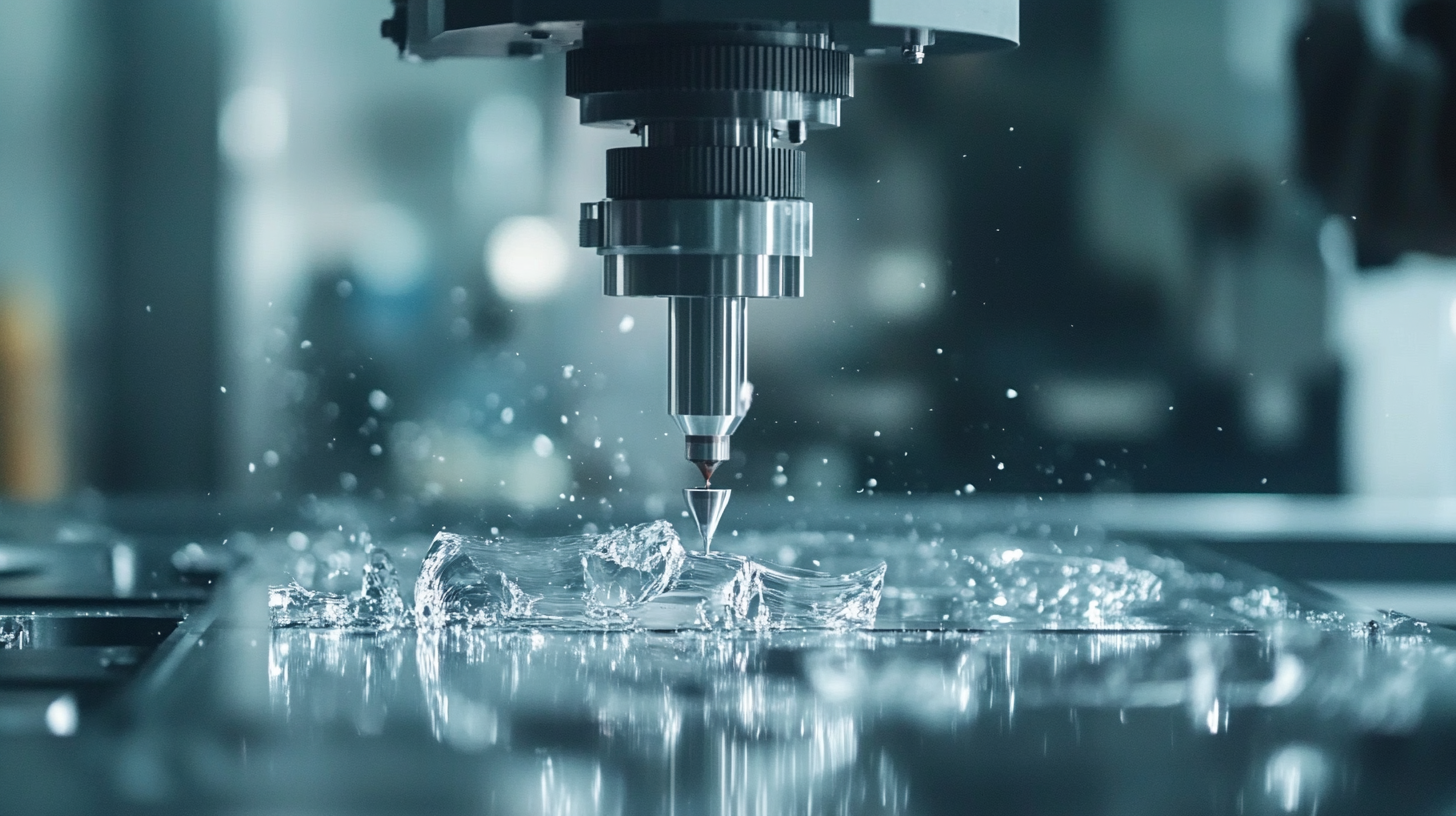
Key Performance Indicators: Measuring Success in Aluminium Manufacturing
In the rapidly evolving landscape of aluminium window manufacturing, key performance indicators (KPIs) serve as essential benchmarks for measuring operational success and efficiency. These indicators not only reflect the quality of the final product but also the effectiveness of the fabrication processes employed. By establishing clear KPIs, manufacturers can identify areas for improvement, optimize resource allocation, and ultimately enhance their overall productivity.
One critical KPI in aluminium manufacturing is the rate of production efficiency, which measures the output relative to the input over a specified period. This metric helps manufacturers gauge the performance of their advanced fabrication machines. By analyzing this data, companies can make informed decisions about machinery upgrades or modifications to workflow, aiming to decrease downtime and reduce waste. Another significant indicator is the defect rate, which directly impacts customer satisfaction. Keeping track of defects allows manufacturers to pinpoint recurring issues, thus enabling them to refine their processes and ensure that the end product meets the highest standards of quality.
Cost per unit is also a vital KPI that reflects the financial health of the manufacturing process. By closely monitoring this metric, businesses can identify cost savings and inefficiencies that may arise during production. Continuous improvement in this area not only benefits the company’s bottom line but also contributes to a more sustainable manufacturing operation. In sum, focusing on these KPIs allows aluminium manufacturers to unlock the full potential of advanced fabrication technologies and maintain a competitive edge in the market.
The Future of Sustainable Practices in Aluminium Window Production
The steel and aluminum industries are pivotal players in the global shift towards sustainable practices. In line with this movement, the increased integration of advanced fabrication machines in aluminum window manufacturing is redefining the efficiency and environmental footprint of the production process. By leveraging innovative technologies, companies can reduce energy consumption and waste, leading to a more sustainable manufacturing cycle.
Recent events, such as the UN Global Compact exhibition in Shanghai, highlight the global commitment to ESG principles. Such gatherings shed light on how various sectors can contribute to a more sustainable future. Notably, companies like ZTE have demonstrated their commitment to these principles, illustrating the substantial role that corporate responsibility plays in shaping a sustainable economy. This emphasis on sustainable practices must also extend to small and medium enterprises, as they are crucial for creating an inclusive and sustainable future.
In the context of aluminum window production, adopting advanced fabrication techniques not only enhances operational efficiency but also aligns with broader sustainability goals. The industry's evolution towards innovative practices echoes the calls for a collective effort towards environmental stewardship. By prioritizing the integration of advanced technologies, the aluminum window sector can emerge as a leader in sustainable manufacturing, paving the way for a greener future.